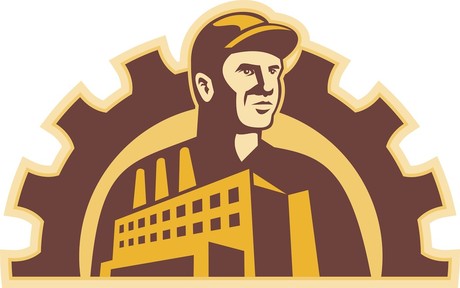
Seven in 10 manufacturing companies in Singapore plan to increase their deployment of Industry 4.0 solutions by 2020 to enhance organisational efficiency and productivity, as well as drive competitive advantage.
The top three solutions they intend to deploy are IT/OT convergence (22 percent), mobility and devices (22 percent), and robotics and artificial intelligence (20 percent).
These are part of Accenture’s Manning the Mission for Advanced Manufacturing report, which surveyed 29 key industry stakeholders in Singapore, including 20 manufacturing companies that represent 64 percent of the republic’s manufacturing output in energy, chemicals and utilities industries.
Since talents with knowledge and skills for industrial internet of things (IIoT) are required to support the move towards Industry 4.0, 75 percent of manufacturers intend to borrow digital capabilities from third-party vendors to serve their short-term needs. Almost two-thirds of them (60 percent) also plan to build critical capabilities internally for long-term self-sufficiency.
The report also revealed that hybrid talents will be key in enabling Industry 4.0.
For instance, more than three-quarters of the respondents said that operators and technicians will need to be able to read and interpret data displayed on performance metric dashboard in future.
“People who can understand the industry and also manipulate data will be a lot more valuable than vanilla-flavoured data analysts who just put data through a machine. They know what the data represents and where the potential vaule in the data exists,” Stephen Fowler, general manager of Shell Jurong Island, told Accenture as part of the study.
Meanwhile, engineers need to show familiarity with “data analytics, network engineering , and cybersecurity to help manufacturers on their advanced manufacturing initiatives,” shared Damian Chan, executive director of Energy and Chemicals, EDB.
To ensure that Singapore has an IIoT-ready workforce, Accenture advises:
- The industry to work closely with the government to identify the technical skills and corresponding knowledge needed across job roles;
- Educational institutions and training providers to develop programmes that can help nurture cross-trained industrial engineers and technicians with digital skills;
- Unions and trade association chambers to jointly support the continued employability of the workforce; and
- Organisations to equip talents that enter the industry with multi-domain capabilities. This should not be done via a one-off course, but through continuous training.
Image credits: GraphicStock | Source: Computerworld Singapore